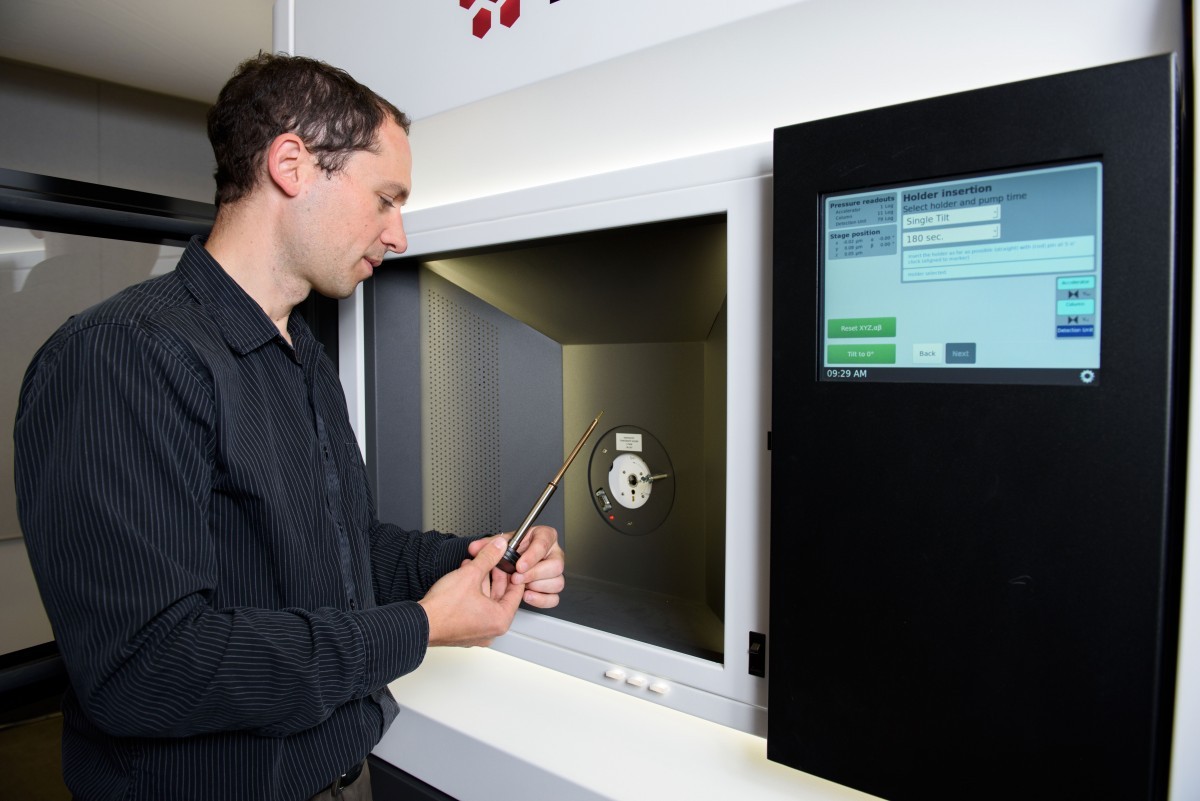
Kevin McEleney, the MIM facility manager, prepares a sample for testing. // Photo by Katie Chalmers-Brooks
Through the lens
The micro-world where big ideas grow
From the Winter 2016 edition of ResearchLIFE:
Derek Oliver says the word “cool” like he’s just spotted a Lamborghini. What the University of Manitoba scientist caught a glimpse of is the inner mechanisms of a giant microscope. He apologizes for the “nerd moment” mid-tour of the renovated space that will soon be home to the Manitoba Institute for Materials (MIM). A technician commissioning the Talos™ transmission electron microscope (TEM) left the side panel off, revealing a roadway of cords, and flashing lights and bolted flanges. It’s a view few in the world have seen.
“Is it open?” asks Oliver, jockeying for a view. “Wow. Oh, cool.”
The microscope is the first of its kind on Canadian soil and one of only 10 across North America. The $16.7 million MIM Facility for Composite and Material Characterization, of which Oliver is director, is scheduled to open this winter with this massive microscope as its main attraction.
The device is so sensitive to vibration and electronic noise that the acoustically sealed room where it’s housed can’t have fluorescent lighting (since it emits tiny amounts of radiation) and the operator has to control the machine remotely from outside. The microscope’s specifications fill a binder four inches thick, and include parameters as specific as how much the ambient temperature can deviate over an hour.
To the layperson, the microscope looks like a futuristic vending machine. To the expert, it is a finely crafted machine that provides incredibly accurate information in 3-D about the spacing of atoms in a sample.
The more scientists know about the molecular makeup of complex materials—be they rock, metal, plant or plastic—the better they can bring ‘the next big thing’ to life.
“Materials are at the core of our modern life,” says Oliver, an associate professor in the department of electrical and computer engineering.
Indeed, materials research is in demand from industry players looking for ways to improve on everyday items, from the pan we cook with to the cellphone we can’t live without.
These new technologies can shape entire sectors, as is the case for aerospace in Western Canada. Some of MIM’s researchers look at new ways to build and test airplane parts to make them stronger yet lighter, which saves on fuel. More than $3 million of the facility’s funding comes from the federal government’s Western Economic Diversification Program and General Electric to boost Winnipeg’s aerospace industry.
To develop high-tech composite materials, scientists must uncover how its molecules and the atoms within are constructed, how they’re linked together, what geometric shape they form. The more they figure out, the more they realize how much they don’t yet know.
“It’s one of those slightly funny, almost paradoxical things, that you suddenly realize in a sense how little you actually do understand,” says Oliver. “Maybe you’re looking at materials we have used for years and years and years and we’re still discovering new information. . .This new information enables you to develop a new product or a better product or a new technology.”
The University of Manitoba formed MIM six years ago. The group is made up of researchers from the Faculties of Engineering, Science, Health Sciences, and Agricultural and Food Sciences, as well as the Clayton H. Riddell Faculty of Environment, Earth, and Resources.
Their area of focus runs the gamut, from engineering new materials that build stronger bridges, to developing the next generation of memory technology for our computers, to using ultrasound to develop the perfect ramen noodle. (Over half of Canada’s wheat exports are used to manufacture Asian noodles.)
“This is a massive market impact,” says Oliver. “It’s a neat illustration of the kind of connectivity that we’re trying to build more of.”
Often facilities are developed around one high-profile researcher but in this case, it’s a multi-million dollar investment in a collaborative approach, bringing together more than 200 faculty, researchers and students university-wide. “This facility breaks the mould because it is an institutional investment,” says Oliver.
To get to the materials research hub, you have to go deep underground: 17 steps below the tunnel beneath Allen Building. It will also have a ground-level entrance in a building-cum-island in the parking lot known as A-Lot, 25 Sifton Road. What for years was a space that stored physics equipment—a decommissioned cyclotron—is now reimagined into a modern mix of instrument rooms and lab space.
Welcome to the land of the little, where the size of a sample is described by how much smaller it is than a human hair. Each of the centre’s three new, world-class electron microscopes have their own unique talent and will be used by researchers in different ways.
Take the environmental scanning electron microscope, which can analyze wet or living samples (even a housefly). Because it requires less of a vacuum, the samples can be examined in their natural state. Geologists can image permafrost—frozen cores of rock, soil or sediments—and their surfaces to see embedded microfossils and better understand and predict global warming. Biological scientists can image the molecular makeup of plants destined to be environmentally friendly plastic.
“We have a lot of plant matter around because we are on the Prairies and there are bits of industry along these lines that we can tap into and want to tap into,” says Oliver.
He’s collaborating with researchers at Caltech and the Florida Institute of Technology to build and modify small rods of silicon. They’re among a large network of labs whose end goal is to develop a device that could use sunlight to split water into its constituent parts: hydrogen and oxygen. Hydrogen could solve the energy needs of developing countries, and, closer to home, oxygen could be generated for medics to give to patients in remote Manitoba communities.
When imaged close-up, these rods resemble tire marks left from a driver doing doughnuts in a desert. Another view looks like an aerial shot of a depleted lumberyard. A third, Oliver notes, reminds him of the kid’s toy that takes the shape of your hand when you press against its plastic spindles. The images can look striking, even beautiful.
A close-up of metal fibres on the NanoSEM scanning electron microscope could be confused for abstract artwork. “Each of these dots is about one two-thousandths of the width of a human hair,” says 6-foot-2 Oliver.
Researchers from the Composites Innovation Centre (a not-for-profit industrial consortium with whom MIM partners) will use the electron microscopes to analyse naturally grown fibres that offer a more sustainable option to fibreglass.
Alongside researchers from biosystems engineering and chemistry, they’re investigating if plant fibres could replace glass fibres to manufacture wing and engine components for planes. (They’ve already shown local manufacturer Buhler-Versatile a tractor hood and fender made of hemp and agave fibres.) These composites would be as strong as metal but much lighter.
College of Dentistry researchers are looking at ways to make dental coatings and fillings last longer. And agriculture researchers are investigating which fungi grow on grain during its storage—in developing countries, where as much as half of harvests can be lost to spoilage.
“Not only are we showing to the outside world how something that might normally sit in the research domain could be useful to them, but we’re showing the students we graduate how the leading edge of research technology can be relevant to different parts of the world,” says Oliver.
Students will learn alongside researchers and industry partners. From the communal area in the heart of the 9,000-square-foot centre, they can check out imaging from the TEM microscope as it happens.
These details matter, insists Oliver. The facility is designed for collaboration and to encourage students to learn by doing.
He points out another detail in the new space—the frosted design on the many glass walls. These series of lines depict a spectrum. Oliver explains it’s a nod to spectroscopy (the study of how matter can be ‘fingerprinted’) and how sunlight is filtered by the atmosphere. Symbolically, this décor touch brings natural light down into the windowless basement space.
“It’s kind of a fun, little thing,” he says.