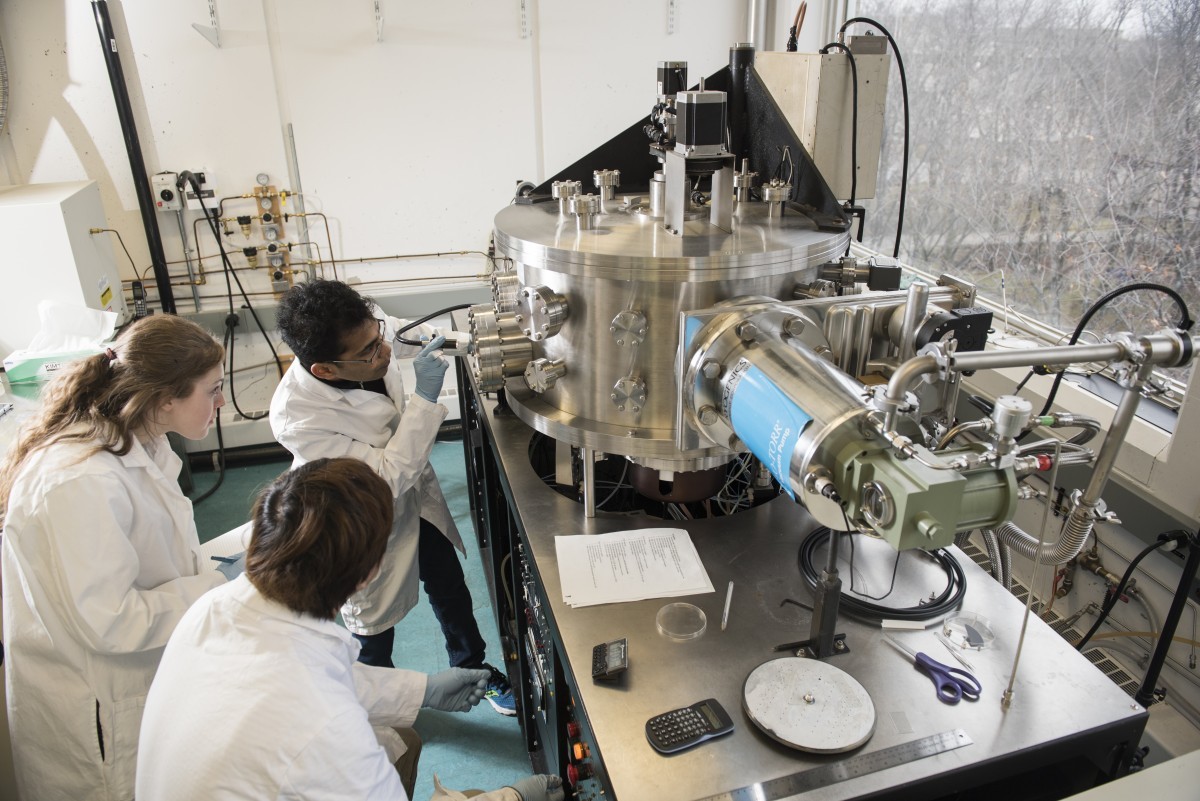
The cleanest room on campus
Where the tiniest machines are made
Cyrus Shafai went against his instinct. He knew he probably didn’t have to buy the small wood sticks to apply the silver glue he was purchasing from the scientific catalogue, but he was a cautious graduate student and thought the sticks might have some special quality. Perhaps they were super clean.
“I ordered them even though I was pretty sure they were just toothpicks. Then they arrived and I looked at them and thought they looked exactly like toothpicks. So I put one in my mouth and it tasted like mint. I bought expensive toothpicks,” the renowned nano material researcher admits.
This lesson stayed with Shafai throughout his research career in the Faculty of Engineering: buy local and build what you can yourself, and invest the savings elsewhere. In 2001, he was looking to purchase an ultra-clean lab, but instead his team decided to build one instead.
That year, three technicians from Electrical and Computer Engineering drove to the University of Alberta to disassemble a clean lab that Micralyne Inc. was scrapping. The parts were loaded onto three freight trucks, and shipped to Winnipeg. Then, Shafai, his students, and the technicians began re-assembling the lab, making trips to Canadian Tire and other hardware stores to purchase parts. The lab has since grown into theNano-Systems Fabrication Laboratory, a key part of the Manitoba Institute for Materials (MIM).
“A lot of time universities put a higher value on the professors,” Shafai says, “but the technicians also have skills that are of high value – they build things and are crucial in training students.”
Interestingly, the purchase of a household-grade washer and dryer to clean the special suits people must wear required some explaining.
“That raised some flags,” Shafai says laughing. “You can order very expensive machines, but a washer and dryer on a purchasing order looks weird.”
This specialized lab is the only facility of its kind in Manitoba and one of only a handful in Canada. With over $4 million of equipment it’s a central facility in the university’s material research network.
Dust has no home here: visitors must wear lint-free suits and the lab’s air is exchanged entirely several times every minute. Even the paper researchers write on is not actually paper but a plastic, since scratching a pen on paper creates dust. It’s quite possible the cleanest air one will ever breathe. “It’s great in allergy season,” Shafai says.
Under the roar of ventilating fans, he researches and builds micromachines, or micro-electronic-mechanical systems, specialized devices used in many areas of life – cars rely heavily on them; your airbag is controlled by one.
They are tiny. A dust particle dwarfs their components, which is why the lab must be so clean. At this scale, a colliding dust particle can destroy what Shafai and his students built.
Shafai builds micromachines that bend mirrors, sense electrical currents, and make small antennas act like big ones – a project he works on with his father, U of M professor Lotfollah Shafai.
“I think my biggest success has been in developing the techniques to build these micro structures,” Shafai says. “Every time we make something we learn something new and then we bring that skill set to make another design. If you came to me 10 years ago and said lets make adaptive optic mirrors, I’d say ‘No.’ But now we have technology that we can tackle the problem. We’ve been working on this for three years and it looks like we can build a functional one.”
Adaptive optics was conceived by astronomer Horace Babcock in 1953. Babcock wanted to solve a problem tormenting his field – twinkling. Stars twinkle because turbulence in the atmosphere distorts their light. Through an Earth-based telescope they look
fuzzy, offering little useful information. Babcock thought-up adaptive optics and today engineers like Shafai have cultivated the knowledge to build the advanced technology.
“I think my biggest success has been in developing he techniques to build these micro structures. Every time we make something we learn something new and then we bring that skill set to make another design.”
How it works: a laser mounted to a telescope shoots into the sky and a computer notes how the light distorts, hundreds of times a second. This information is used to instantly move hundreds of actuators under a dime-sized mirror. The actuators act like pistons,constantly pushing and pulling the surface of the mirror, altering its shape to counteract the atmosphere’s turbulence. Voila, astronomers get a clear view, something normally reserved for space-based telescopes like Hubble.
This technology can also be used to help image the retina in human eyes, where image quality is affected by aberrations when trying to look inside the eye. Adaptive optics can correct this and allow doctors to see parts of the eye much clearer.
But common adaptive optics systems need a lot of voltage to move the actuators, and each is hooked up to its own wire, resulting in thousands of wires running from the
machine to an external power source resulting in an expensive and relatively bulky, inelegant, contraption.
Shafai improved this design in two ways. First, he made the mirrors bigger and out of polymer rather than metal, making them more flexible and thus lowering the energy
needed to warp them. But the big change was using tiny, low voltage magnetic actuators.
Working with U of M Physics and Astronomy professors Jayanne English and Jason Fiege, Shafai micromachined a system wherein small coils run under the mirror segments. When electricity runs through the coil, the magnetic field generated pulls the mirror segment down. This method uses far less voltage and far fewer wires. In fact, Shafai can build the mirror and the circuitry onto the same chip, opening the possibility of mass-producing them quickly and cheaply.
“So that’s our adaptive optics system,” he says. “We’re hoping it works. We’ve done the design work already and this year we have been trying to build some prototypes in the lab.”
The Nano-Systems Fabrication Lab, however, does more than just build tiny machines. Nearly 300 different professors and students have used the lab. It is an open-access facility, where you can rent time on machines by the hour. Want to put a gold coating on a wafer? You can get it done here. The lab also has one of the most sophisticated chemical areas on campus and Shafai encourages others to use it rather than spend the time and money setting up their own.
“We all have our skill set,” Shafai says. “For many projects you need another person to bring skills you don’t have. MIM, I think, helps bring everyone together. You become aware of the existence of capabilities through MIM. You might not have otherwise known that in that building over there they can do these cool things.”