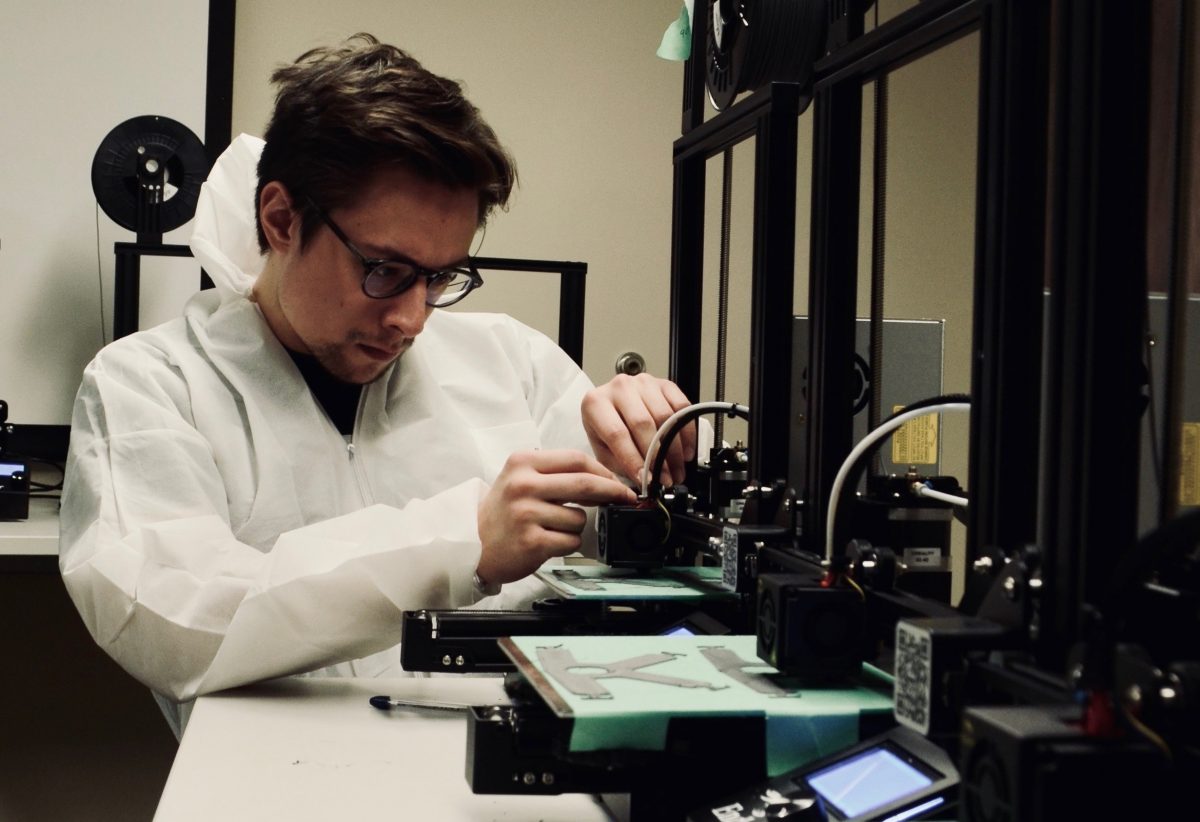
Jakob Weirathmueller uses a 3D printer to create a reusable silicone face mask.
Medical student using 3D printing skills to make face masks
A second-year Max Rady College of Medicine student is using his 3D printing experience to help a group of physicians develop reusable silicone face masks to be used to protect health-care workers from COVID-19.
When Jakob Weirathmueller found out that Dr. Christian Petropolis, program director of the University of Manitoba’s plastic surgery residency program, and Dr. William Turk, an ophthalmologist, were developing a reusable silicon face mask he knew he had to volunteer to help out.
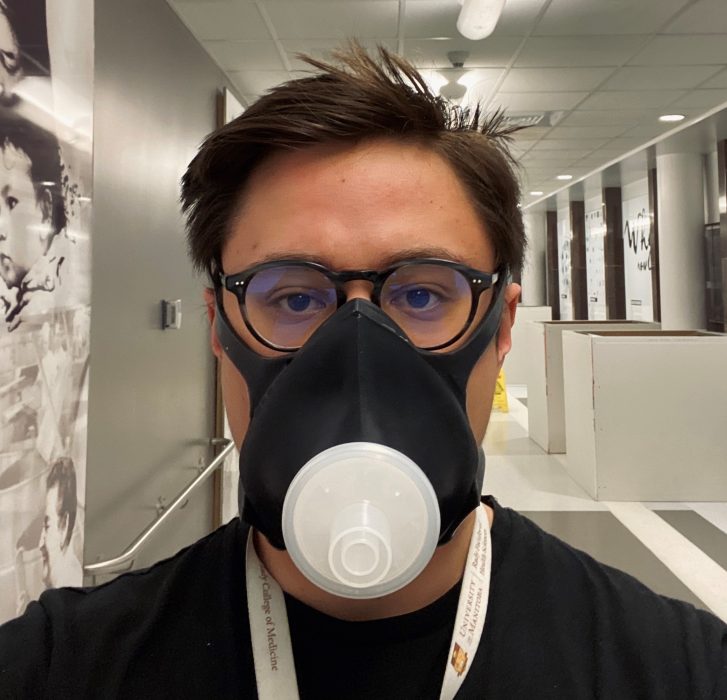
Jakob Weirathmueller wears one of the reusable face masks he is helping make.
“It felt like the right thing to do,” he said. “It seems that this is the best way I can use the skills I have at my disposal. I went into medicine to help people, so it just makes sense to find the thing that I can do to use my skills and be the most helpful possible.”
For the past two years, Weirathmueller has developed his 3D printing and 3D design skills by helping physicians build surgical models for eye surgery and breast reconstruction surgery. A surgical model allows medical students and residents the chance to practice their skills on a non-living subject.
Petropolis said that Weirathmueller’s largest contribution to the mask-making project has been in the area of managing the 3D printers.
“Making sure all the prints are running smoothly and performing maintenance on the printers is a time-consuming process, so this work has freed up our time to focus on other manufacturing and design elements,” Petropolis said. “Jakob is now helping with production as well as learning some of the design tools.”
Weirathmueller has handled all the 3D printing by keeping 23 printers up and running. They can assemble up to 100 masks per day, he said.
“Seeing all of my fellow med students putting in so much work, and all the incredible volunteering that has been going on, has just been a huge inspiration for me and makes me want to work even harder to do my part,” he said.
Weirathmueller has definitely been doing his part. His longest stretch of work on the project was 52 hours with just two hours of sleep and he’s put in a few 20-hour days.
“It’s definitely a test of endurance,” he said.
The masks, which a filter is inserted into, are now being used at Winnipeg hospitals and the goal is to have a company take over production and mass produce the masks, Weirathmueller said.
Not only is Weirathmueller receiving the satisfaction of doing his part in the fight against COVID-19, he is gaining some valuable experience. He’s improved his 3D printing and 3D design skills, which he hopes to merge with his future career as a physician.
“I’m the happiest when I’m able to build things that can make a difference,” he said. “So whatever area I go into in medicine I really do plan on continuing to build and make things that have a meaningful impact on the world around me and the people I’m treating.”